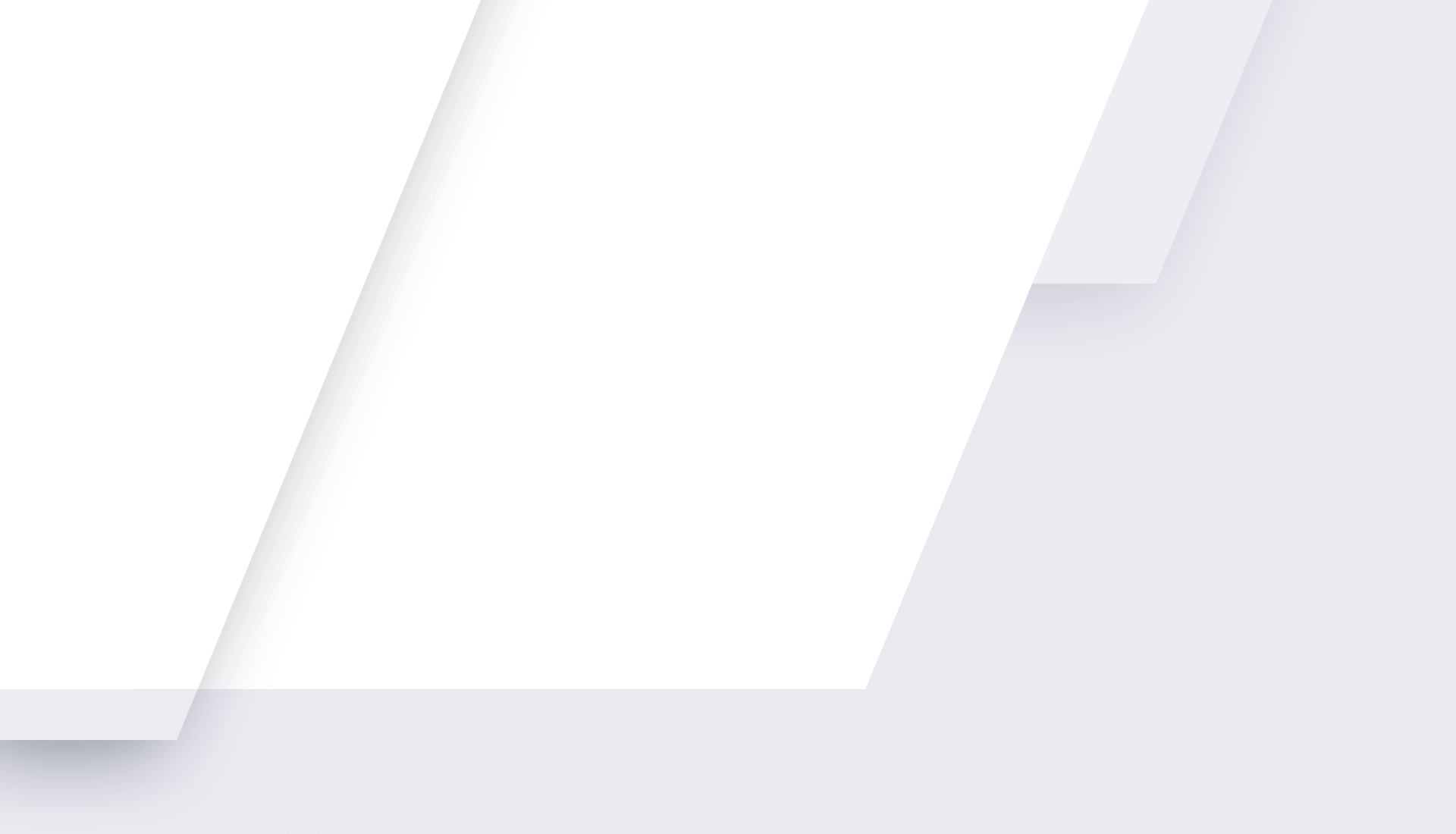
Maintenance
Regular maintenance of your boiler plant helps minimise breakdowns and service interruptions.
our service
Its vitally important that your equipment is kept in pristine working condition, which in turn minimises downtime and loss of income and productivity.
Because our team values quality and safety, all vessels that leave our factory are supplied with a data book consisting of the following:
- Third party pressure test certificate and certificate of compliance.
- ISO quality control plan.

Our Maintenance Checklist
Periodic Maintenance
These items should be addressed by the building’s maintenance staff on a continual basis, or as often as indicated below:
- Check and maintain proper oil level in compressor lube tank (daily). Use SAE 20/30 oil.
- Clean oil filters at least twice a week:
– Shut-off power to pump motor.
– Close shut-off valve.
– Pull out filter. Clean filter and re-insert into housing.
– Place strainer cap into proper position, restart pump motor, and check vacuum.
– Vacuum reading must be high; if not, check seal on cap. If reading is high, then open oil valve.
– Check oil pressure reading at the burners. - Keep sight glasses clean. This allows for a clear view of the burner flame and any carbon build-up on the boiler’s combustion chamber (as needed).
- Keep air filters clean. A clogged air filter can lead to poor air/oil mixture and carbon build-up (as needed).
- Check oil circulation temperature at sidearm pre-heaters. Inlet temperature should be 40° C to 50° C, and outlet temperature should be 60° C to 65° C for No. 6 oil (daily).
- Flush drain low water cut-offs/sidearm oil pre-heater (twice a week).
- Flush drain low water cut-offs while burner is on and a flame is present in the boiler’s combustion chamber. When the unit is flushed, the flame should turn off. Allow the burner to start before checking other low water cut-offs.
- Flush down water-line heater, shut off lower isolation valve, open drain valve to flush unit, shut drain off valve, and reopen isolation valve.
- Conduct boiler bottom blowdown to clear sludge and sediment, control high water, and control chemical treatment concentrations (monthly or as needed).
- Monitor the make-up water being added to the boiler and/or the boiler feed unit. Since the system operates via closed loop, an excess amount of fresh (untreated, oxygenated) water supply is detrimental to boiler components and is often a sign of a leak in the system.
- Monitor smoke alarm on a weekly basis:
– Wipe light source and receiver.
– Smoke alarm unit should not be set at its highest point.
– Unit should be set in accordance with NYC Buildings Department standards. - Maintain a rigorous boiler chemical feedwater treatment programme.
- Maintain a boiler room log to record any problems and routine maintenance.
- Check combustion, inspect burner controls, and inspect burner operation.
- Conduct trap inspection program with replacement of trap elements in apartment units and steam traps within the cellar.
- Conduct pipe inspection program to ensure all pipes are pitched in the direction of steam source (one-pipe steam systems) or condensate drainage (two-pipe systems).
Annual Maintenance
- Inspect and clean fireside surfaces.
- Inspect all burner refractory material.
- Inspect all manhole gaskets for leaks.
- Inspect and test all system valves.
- Inspect and test all safety valves.
- Clean and rebuild low water cut-off.
- Recalibrate all operating controls.
- Overhaul feed water pumps.
- Clean condensate receiver.
- Inspect electrical terminals.
- Switch boiler automation to summer mode.
- Check fuel and oil levels.
- Clean and inspect chimneys.
- Clean and tune boiler and components.
Why Do I Need Cyclotherm's Solutions?
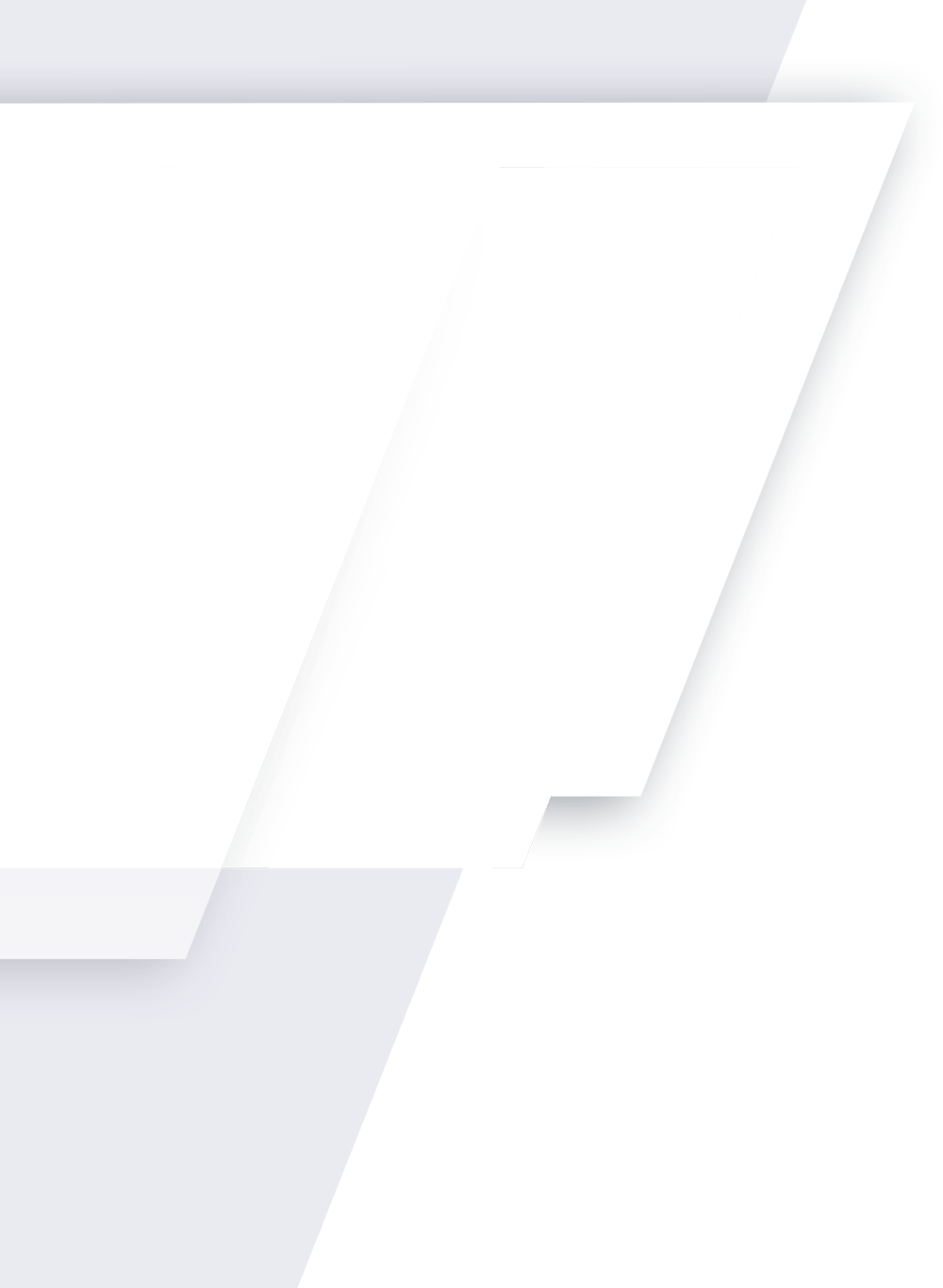
patented technology
We manufacture a comprehensive range of Heated Boiler solutions with our patented heating solution.
quality manufacturing
Our quality of material and manufacturing processes ensure you get the end product you expect.
breakdown service
We know and understand our clients needs to be kept up and running and the cost of having their system down, which is why we have emergency services available.
Proudly South African
We are a home grown South African company founded in 1970.
Affordable solutions
When it comes to longevity, our product outlasts anticipated life spans and stands up extremely well against the test of time. Many of our systems are still running 40+ years later.
maintenance
We have dedicated teams qualified in ensuring you are kept up and running.
Sales Request Form
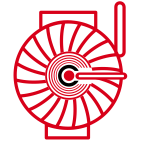
Industrial Autoclaves
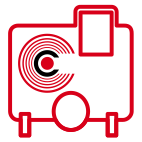
CALORIFIERS
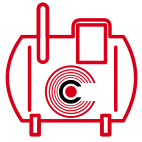
PRESSURE VESSELS
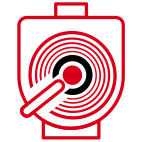
Steam Generators
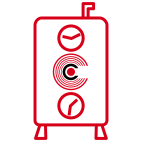
HOT WATER STORAGE HEATERS
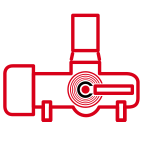
Electrical Hot Water Heater
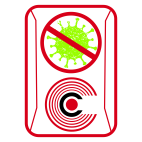
STERILIZATION BOOTHS
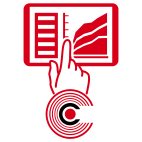